Gia công chi tiết dạng trục là quy trình phổ biến trong lĩnh vực cơ khí bởi các sản phẩm dạng trục được ứng dụng trong rất nhiều ngành công nghiệp hiện nay. Vậy quy trình gia công chi tiết dạng trục như thế nào? Mời các bạn theo dõi bài viết sau đây của cơ khí KCC.
Tìm hiểu về chi tiết dạng trục
Chi tiết dạng trục – trục vít là chi tiết không thể thiếu của nhiều chi tiết máy trong ngành cơ khí chế tạo máy. Trục vít chủ yếu được dùng trong các bộ truyền chuyển động và truyền công suất cho 2 trục chéo nhau. Góc giữa 2 trục thông thường là 90 độ (bộ truyền trục vít) và chúng dùng để biến chuyển động quay thành chuyển động tịnh tiến.
Bộ truyền trục vít – bánh vít có khả năng truyền công suất và chuyển động có tỷ số truyền lớn, có khả năng tự hãm và làm việc không ồn ào. Trục vít được biết làm việc trong điều kiện bôi trơn, khó khăn trong việc làm mát. Do đó, trục vít sinh ra nhiệt khi làm việc và chúng cũng là nguyên nhân gây hỏng gồm các dạng mòn răng và dính răng.
Do điều kiện khó khăn như trên nên các chi tiết dạng trục cần có biện pháp công nghệ thích hợp. Quy trình công nghệ gia công cần phải cẩn thận để nâng cao tuổi thọ của chi tiết dạng trục.
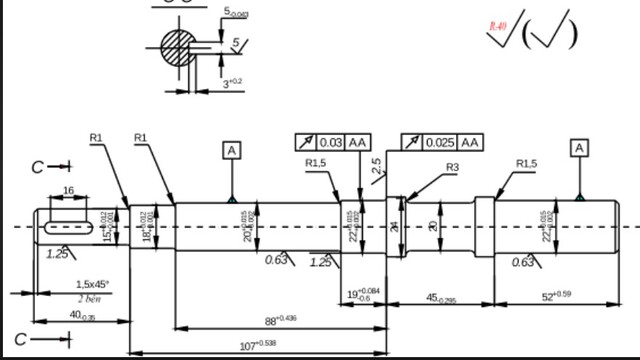
Quy trình gia công chi tiết dạng trục
Để gia công chi tiết cơ khí có độ chính xác cao, ta phải có một quy trình công nghệ đúng đắn. Phân chia hợp lý các nguyên công để đảm bảo được nâng suất ví dụ như nguyên công nào thực hiện trước, nguyên công nào thực hiện sau.
Tùy vào điều kiện sản xuất của chi tiết mà ta có nhiều cách để thực hiện các bước công nghệ khác nhau. Cụ thể, quá trình gia công chi tiết dạng trục được tiến hành như sau:
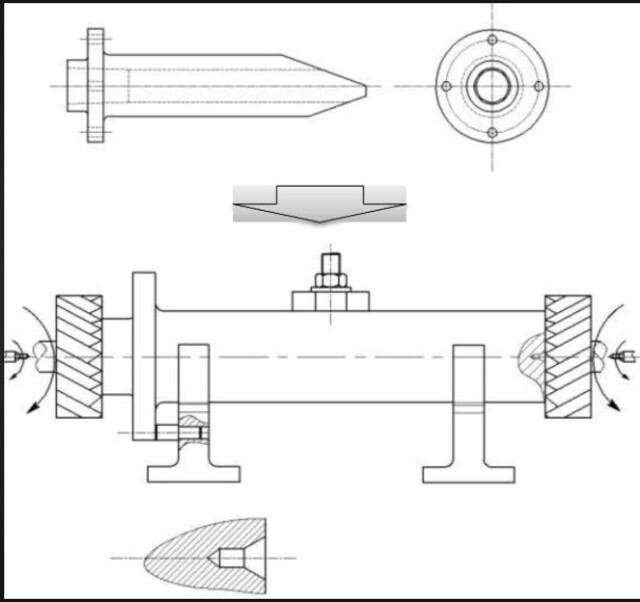
Chuẩn bị phôi
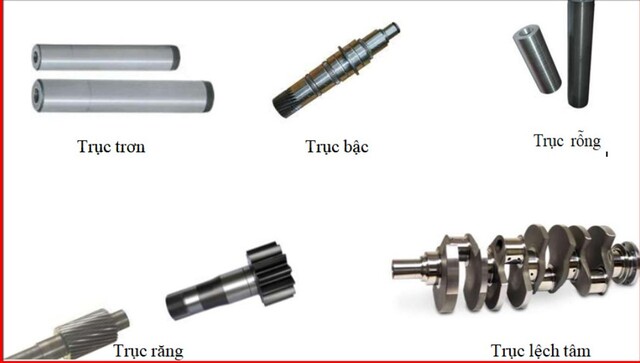
Trước khi vào quy trình gia công chi tiết dạng trục, ta cần xác định phôi. Xác định phôi hợp lý sẽ giảm sức lao động, mức tiêu hao vật liệu, đảm bảo tính năng kỹ thuật của máy, rút ngắn quy trình công nghệ. Việc chọn phôi sẽ căn cứ vào các yếu tố như:
- Hình dáng, kích thước, kết cấu của chi tiết gia công.
- Cơ tính, vật liệu, yêu cầu kỹ thuật của vật liệu.
- Dạng sản xuất
- Hệ số sử dụng của chi tiết, vật liệu.
Theo đó, ta sẽ có những phương pháp chế tạo phôi như sau:
- Phôi đúc: Đây là phương pháp chế tạo phôi mà trong quá trình sản xuất sẽ nấu chảy hợp kim, kim loại rồi rót vào lòng khuôn đã được tạo sẵn.
- Phôi cán: Đây là phương pháp cho kim loại biến dạng giữa trục cán ( 2 trục quay ngược chiều nhau) có khe hở nhỏ hơn chiều cao của phôi làm giảm chiều dài, tăng chiều rộng phôi.
- Phôi rèn: Đây là phương pháp gia công bằng áp lực trong đó rèn sẽ khiến vật liệu biến dạng dần về các hướng mà không bị khống chế bởi bề mặt nào khác, chỉ tiếp xúc trực tiếp với bề mặt gia công.
- Phôi dập: Đây là phương pháp dập thể tích hay gọi theo cách khác là dập khuôn. Phôi sẽ bị biến dạng khi gia công bằng áp lực và sự biến dạng của chúng sẽ được giới hạn trong lòng khuôn.
Phôi sau khi hoàn thành cần được kiểm tra về kích thước, hình dạng và các khuyết tật bề mặt để đảm bảo rằng nó đáp ứng các yêu cầu kỹ thuật.
>> Xem thêm: Tìm hiểu quy trình công nghệ gia công chi tiết dạng hộp
Gia công thô
Gia công thô là bước tiếp theo, nhằm loại bỏ lượng vật liệu lớn từ phôi để tạo ra hình dạng cơ bản của chi tiết.
Phương pháp gia công: Gia công thô thường sử dụng phương pháp tiện hoặc phay. Trong đó, tiện là phương pháp phổ biến nhất cho các chi tiết dạng trục.
Cắt sâu: Trong giai đoạn này, các thông số như tốc độ cắt, độ sâu cắt và lượng chạy dao được thiết lập để tối ưu hóa quá trình gia công.
Kiểm tra kích thước: Sau khi gia công thô, chi tiết cần được kiểm tra kích thước để đảm bảo rằng nó gần đạt yêu cầu thiết kế.
Gia công tinh
Gia công tinh là bước quan trọng để đạt được độ chính xác cao hơn và bề mặt mịn màng hơn cho chi tiết.
Phương pháp gia công: Gia công tinh có thể được thực hiện bằng các phương pháp như tiện tinh, phay tinh hoặc mài.
Điều chỉnh thông số: Các thông số gia công như tốc độ cắt, lượng chạy dao và độ sâu cắt cần được điều chỉnh để đạt được độ chính xác cao.
Kiểm tra độ chính xác: Sau khi gia công tinh, chi tiết cần được kiểm tra kỹ lưỡng về kích thước và hình dạng để đảm bảo đáp ứng các tiêu chuẩn kỹ thuật.
Hoàn thiện bề mặt
Bước hoàn thiện bề mặt nhằm cải thiện chất lượng bề mặt của chi tiết, tăng độ bền và khả năng chống ăn mòn.
Mài: Phương pháp mài thường được sử dụng để đạt được độ nhẵn bóng cao. Mài có thể được thực hiện bằng máy mài hoặc mài tay tùy thuộc vào yêu cầu.
Xử lý bề mặt: Có thể áp dụng các phương pháp xử lý bề mặt khác như đánh bóng, phủ lớp chống ăn mòn hoặc sơn để bảo vệ chi tiết.
Kiểm tra bề mặt: Sau khi hoàn thiện, bề mặt của chi tiết cần được kiểm tra để đảm bảo đạt yêu cầu về độ nhám và tính chất bề mặt.
>> Xem thêm: Đơn vị gia công đồ gá chất lượng, giá rẻ
Các phương pháp gia công được sử dụng
Trong quy trình gia công chi tiết dạng trục, có nhiều phương pháp khác nhau được sử dụng, bao gồm:
- Phay: Phay là phương pháp gia công sử dụng dao phay để loại bỏ vật liệu. Phương pháp này thường được sử dụng để gia công các bề mặt phẳng hoặc các rãnh trên chi tiết.
- Tiện: Tiện là phương pháp gia công chủ yếu cho các chi tiết dạng trục. Dao tiện sẽ quay quanh phôi để cắt bỏ vật liệu, tạo ra hình dạng tròn và các bậc khác nhau.
- Mài: Mài là phương pháp gia công cuối cùng để đạt được độ chính xác cao và bề mặt mịn màng. Mài thường được sử dụng để hoàn thiện các chi tiết có yêu cầu cao về độ nhẵn và độ chính xác.
Mỗi phương pháp gia công có ưu điểm và nhược điểm riêng, và việc lựa chọn phương pháp phù hợp sẽ phụ thuộc vào yêu cầu cụ thể của từng chi tiết dạng trục.
Yêu cầu kỹ thuật đối với chi tiết dạng trục
Chi tiết dạng trục là một trong những thành phần quan trọng trong cơ khí và chế tạo máy. Để đảm bảo hoạt động hiệu quả và bền bỉ, các chi tiết này cần đáp ứng nhiều yêu cầu kỹ thuật khác nhau. Dưới đây là các yêu cầu chính liên quan đến kích thước và dung sai, độ chính xác hình dáng, độ nhám bề mặt, và tính chất cơ lý của chi tiết dạng trục.
Kích thước và dung sai
Kích thước danh nghĩa: Kích thước danh nghĩa của chi tiết dạng trục được ghi trên bản vẽ kỹ thuật và là cơ sở để tính toán các sai lệch kích thước. Ví dụ, đường kính các cổ lắp ghép thường yêu cầu đạt độ chính xác cấp 7 đến 8.
Dung sai: Dung sai cho phép các sai lệch trong kích thước của chi tiết. Đối với chi tiết dạng trục, dung sai đường kính cổ trục có thể nằm trong khoảng từ 0.25 mm đến 0.5 mm. Điều này giúp đảm bảo rằng các chi tiết có thể lắp ghép chính xác với nhau mà không gây ra sự cố trong quá trình hoạt động.
Độ chính xác vị trí: Yêu cầu về độ chính xác vị trí giữa các bề mặt cũng rất quan trọng. Ví dụ, sai lệch của cổ trục ren so với tâm chung của trục cho phép trong giới hạn 0.05 đến 0.1 mm.
Độ chính xác hình dáng
Hình dạng hình học: Đối với chi tiết dạng trục, độ chính xác hình dáng hình học như độ côn, độ ô van cần được kiểm soát chặt chẽ. Độ không đối xứng của các rãnh hoặc bề mặt cần đảm bảo không quá 0.03 mm trên 100 mm chiều dài.
Độ vuông góc: Độ vuông góc giữa các bề mặt cũng là một yếu tố quan trọng, không được vượt quá 0.05 mm trên 100 mm chiều dài. Điều này đảm bảo rằng các bề mặt của chi tiết có thể tương tác chính xác với các chi tiết khác trong hệ thống.
Độ nhám bề mặt
Yêu cầu về độ nhám: Độ nhám bề mặt của chi tiết dạng trục ảnh hưởng lớn đến khả năng làm việc và tuổi thọ của chi tiết. Bề mặt ngõng trục cần đạt độ nhám Rz = 40, trong khi các bề mặt còn lại yêu cầu độ nhám Rz = 2.5.
Bề mặt ren: Bề mặt ren cũng cần được gia công đạt độ chính xác cao, thông thường yêu cầu đạt độ chính xác cấp 7 đến 8. Độ nhám của bề mặt ren ảnh hưởng đến khả năng lắp ghép và độ bền của chi tiết khi hoạt động.
Tính chất cơ lý
Độ cứng: Tính chất cơ lý của chi tiết dạng trục rất quan trọng, đặc biệt là độ cứng sau quá trình nhiệt luyện. Độ cứng cần đạt từ 45 đến 50 HRC để đảm bảo chi tiết có khả năng chịu tải tốt trong quá trình làm việc.
Tính bền: Chi tiết dạng trục cần có khả năng chịu lực và mài mòn cao. Vật liệu được chọn cho chi tiết thường là thép hợp kim hoặc thép cacbon, có tính chất cơ lý tốt để đáp ứng yêu cầu làm việc.
Tính công nghệ: Các bề mặt của trục cần được thiết kế sao cho có thể gia công dễ dàng và hiệu quả. Điều này bao gồm việc lựa chọn phương pháp gia công phù hợp và đảm bảo rằng chi tiết có độ cứng vững cần thiết trong quá trình hoạt động.
Mọi người vừa được tìm hiểu về quy trình công nghệ gia công chi tiết dạng trục qua bài viết trên rồi. Mong rằng những chia sẻ này sẽ mang đến nhiều thông tin bổ ích cho người xem. Các bạn nếu có nhu cầu tìm hiểu và đầu tư các thiết bị cơ khí đừng quên tham khảo sản phẩm tại cơ khí KCC nhé.
ID bài viết: 193197